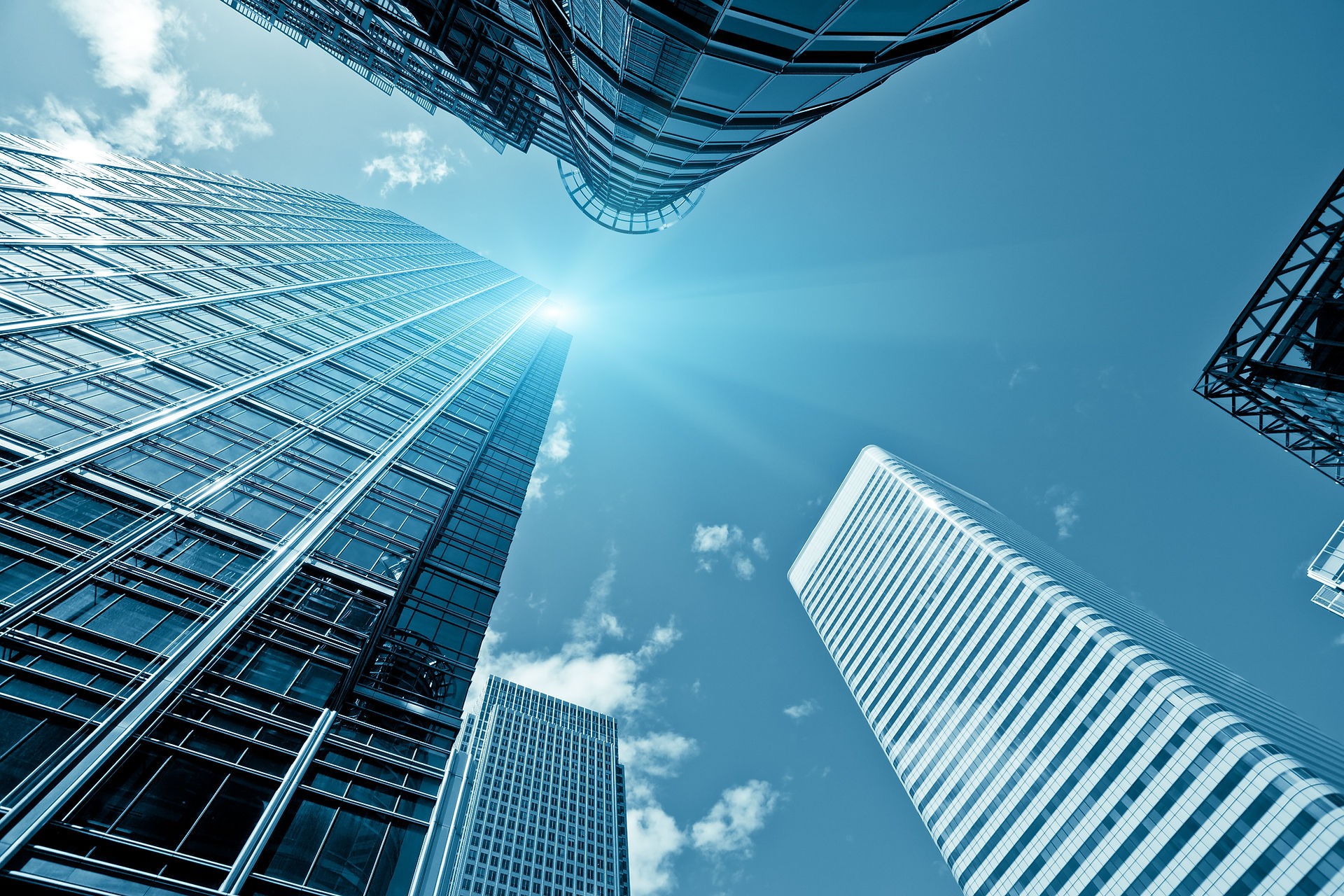

Alec Newton
Plastics and Composites Engineering Student
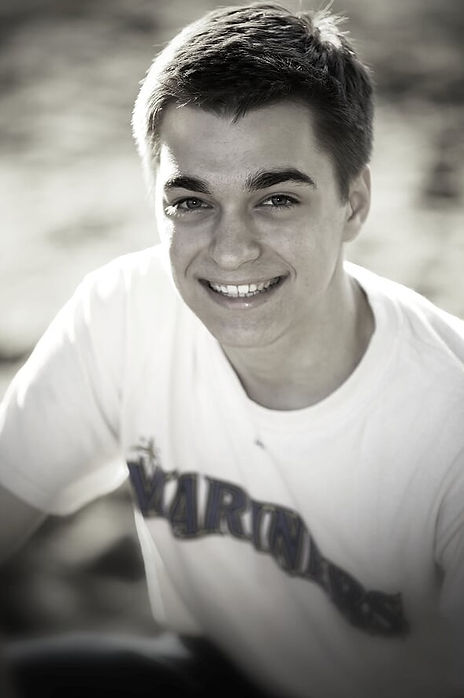
About Me
Education
In my final year at Western Washington University, I am on track to graduate in June 2022 with a Bachelors of Science in Plastics and Composites Engineering as well as a Mathematics minor. The Plastics and Composites major is a combination of both Manufacturing Engineering and Chemistry in which students study the relationship between molecular structure, material properties and performance, the manufacturing of polymers, and composite materials. Courses include CNC machining, Injection Molding Processes, CAD Design, Polymer and Organic Chemistry.
Personal Strengths
All my life I have been someone that has a strong work ethic. In a job setting, I am always someone that gives 110% whether I am working with or for someone. I put my all into my work when people are relying on me to do well, which is where I have become stronger in succeeding while under pressure. One thing that has helped me succeed is by having good organizational skills and time management because it allows me to not fall behind and struggle.
Hobbies/Interests
-
Engineering Design
-
Manufacturing
-
Driving/Racing
-
Sports
-
CAD Modeling
-
Injection Molding
CAD Surfacing Projects in CATIA
-
Kayak: The focus for this project was to model a kayak using wireframe geometry that allow for the outer surfaces of the kayak to be smooth and maintain tangency. Steps for this included marking points in 3D space to locate edge points, connecting the created points to define profile sketches along the length of the kayak, and various surfacing features to smoothly connect the multiple sections.​
-
Car Body: The car body project was a 4 person group project where each person was responsible for a different section on the car, and the goal of the project was to work with your group to ensure smooth connections between each section so the result would be accurate and clean. My specific section for this project was the side of the car, below the windows and everything between the head lights and the tail lights. I'm also responsible for the rear wing, which was simulated in Solidworks Flow Analysis and mine was chosen because it was more efficient than the other designs my group members created.
-
Bottle: The purpose of this assignment was to give experience using wireframe, surface elements and operations in creating a surface model of a plastic bottle. It was also a requirement to organize the model by creating geometrical sets for different elements/sections used in the design.
-
Spoon: For the final project of the CAD using surfaces class we were required to model a spoon of ours using 3 different views such that an accurate model could be made from a front, side, and top view of the spoon. The focus was on overall shape and likeness compare to the real spoon.
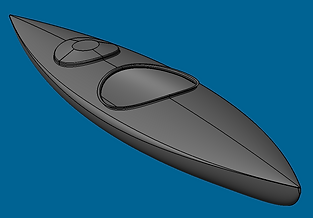

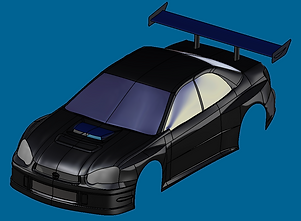






Schoolwork and Projects

Bicycle Crank Set Assembly in CATIA
Project guidelines were to model and replicate 9 parts of a bicycle crankset assembly from a given set of drawings of the parts. Pictured to the right is the crank set assembly model created by me of the exact parts I modeled. All of my CAD drawings associated with this project are attached in the PDF.
WWU FSAE Racing Club

What is WWU FSAE?
The Western Washington University FSAE Club (WWU Racing) is a team of students of all focuses who are passionate about furthering their knowledge and passions through the project of developing a formula–style race car. The team's engineers learn how to operate CAD systems and how to analyze data to make changes to optimize car systems. The Society of Automotive Engineers (SAE) has hosted an annual competition known as Formula SAE (FSAE) for 40 years. The competition allows teams to test their cars and business practices against other cars built by students from across the globe. The team is responsible for the complete design, manufacturing, testing, and competition aspects of building a racecar.
My Roles
I joined the team in the fall of 2019 after hearing about the club from fellow classmates and people outside campus that were familiar with the team. At this time I was focused on the manufacturing phase and this is where my interest began to grow. After being forced online in early 2020, the team faced some tough decisions but ultimately resulted in my promotion to Aerodynamics Lead in the summer of 2020. I was the Aerodynamics Lead for our team from August 2020 until May of 2021, where I was then promoted again to the highest position on the team of Project Manager for the 2021-2022 school year.
​
Aerodynamics Team Member (Sep 2019 - Aug 2020):
-
Practiced designing 3D printed ribs whose purpose was to give a skeletal structure to the front and rear wings. Total number of parts creating internal skeleton was upwards of 40, 5 of which I was responsible for.
-
Responsible for the fabrication of various metal brackets and tabs for components to mount to on the car's chassis. I also manufactured a tool from a sheet of aluminum to be used when doing the layup for the front wing endplates.
-
I was lucky enough to get composite work consisting of measuring and cutting Toray T700 Carbon Fiber Prepreg prior to layups for things such as the skins for the wings. I was also able to aide in the construction of a tool, that resulted in a large scale wet layup creating the cars undertray that measures approximately 24 sq feet in size.
-
Attended weekly meetings to follow along with what the rest of the team was doing and engage with more people.
​
​
​
​
​
​
​
​
​
​
​
​
​
Aerodynamics Co-Lead (Aug 2020 - May 2021)
-
Conducted research and created documentation of relevant aerodynamic behaviors in cars highlighting flow separation, laminar vs turbulent flow, drag vs downforce, effects of low and high pressure zones, and ground effects. This research was an introduction for me to gain the knowledge needed to optimize design of the aerodynamic devices on a formula style racecar.
-
Starting from scratch, I was able to teach myself how to effectively use simulation software such as Simscale and Paraview. With this, I was able to redesign the previous teams rear wing by simulating various airfoils and choosing the most efficient one based on the coefficients of drag and lift. At the time, I was the only person who had the skills to do simulations such that I simulated driving airflow across individual aerodynamic components as well as the entire car to analyze the interactions between each other. With this knowledge, I was essential in helping our powertrain system simulate cooling effects across the accumulator cells of our newest electric vehicle to ensure that the battery was being adequately cooled given conditions such as the accumulator container material, airflow speed, ambient temperature, and the cell modules heating up over an extended period of time.
-
Every year when our team designs a new car, we are responsible for the complete modeling creation of between 1500 and 2000 individual parts. Specifically in this role, I was responsible for the design of the aerodynamic system which ended up being upwards of 170 unique CAD models including but not limited to 34 wing ribs, 10 wing skin surfaces, the entire undertray, and the mounting brackets/points and hardware. Designing in this application required consistent communication between other systems to ensure there was no clashing, as well as frequent and extensive time examining the SAE rulebook to make ensure that our designs would pass all rules.
-
I was able to prove effectiveness in an aero package through improving downforce production from 96.67lbs to 106.47lbs and decreasing the drag from 51.62lbs down to 48.08lbs. Both of the new downforce and drag values were significant improvements from the previous team's car. Improvements were expected to result in faster lap times and greater traction during cornering.
-
Presented the entire aerodynamics design of the teams 2019-2020 car online at the 2020-2021 SAE design event. Despite not designing that specific car, I was able to effectively give a professional presentation and prove my understanding of the system at a high technical level.
​
​
​
​
​
​
​
​
​
​
​
​
​
​
​
​
​
​
​
​
​
​
​
​
​
​
​
Project Manager (May 2021 - Present)
-
Managed a team of 30+ members on a daily basis to build a Formula SAE car over the 2021-2022 school year. Frequently organized and lead team meetings that focused on team goals and deadlines, system updates and weekly progress, and diminishing team conflict.
-
Development of team plans, and timelines created based on success from previous teams, alumni and advisor advice/recommendations, and knowledge of the current team's skill level/experience. Timelines were also structured around specific dates for the SAE competition in June 2022 that had hard deadlines like competition registration and several design document submissions.
-
Had to learn to effectively and accurately communicate between our team, school advisors and engineering department, sponsors, and more. This required me to quickly get over my lackluster communication skills in order to give the team what they needed to succeed.
-
After everyone was forced to move online for the remainder of 2020 and into 2021, our team was unable to effectively recruit more members like it had in the past. The team dwindled down to around 15 key members, and also lost more due to graduation. I quickly reached out to those who had expressed interest in joining from our team website, and also directly played a part in nearly 200 people showing interest in the team at the club info fair that our university puts on every year.
-
Team preservation became a big focus once we moved online and becoming Project Manager, I took on the responsibility of not only rebuilding the team to where it was in 2019, but also planning ahead to ensure the team is setup for success 5+ years down the road.
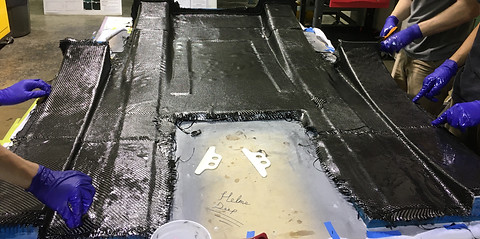

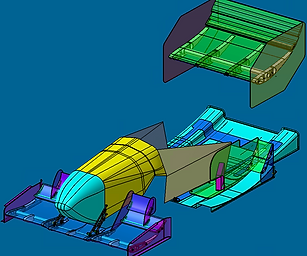

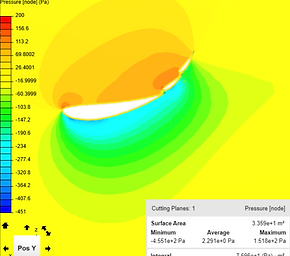
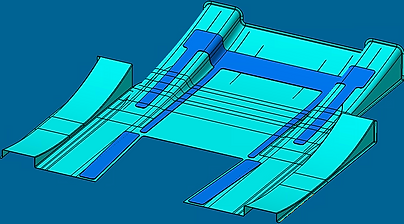


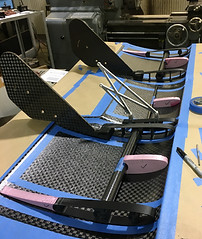
Directed Research with Composites
Starting in September of the 2021 school year, I spent time working on a research project within our school's Plastics and Composites Engineering labs. The focus of the project was finding a way to recycle cured carbon fiber prepreg, such that the carbon fibers could be reused. At the time I joined the research, the previous team had already determined a way to chemically detach the cured epoxy resin from the fibers. In my role, I was helping to scale up the project and maximize efficiency using a 1-liter vessel before moving to a larger 20-liter mixing set up.
​
The problem the previous team encountered was that during the mixing process, the fibers would slowly separate and stick to the side of the vessel and up out of the solvent that was supposed to break them apart. This caused for longer mixing times because of the need to manually push the fibers down in to the solvent. Once introduced to this problem, I was able to design a cap-like piece that would sit on top of the mixture and help keep the fibers down in the solvent in an effort to drastically reduce mixing time.
​
I designed another part to go underneath the cap that will help mix the fibers more and hopefully speed up the mixing time by even more. These prototype parts were printed in PLA that is readily available to our program, and then when we finalized the dimensions and printed the final part in PEEK because it is the only material that was not expected to degrade in the solvent we are using in the mixtures. However, the PEEK completely degraded in its first reaction which caused for us to switch to a stainless-steel version of our stirring apparatus.
​
Future plans for this research include characterizing this material using SEM (scanning electron microscopy) and TGA (thermogravimetric analysis) for analyzing the recovered fibers that are coming out of reactions and ensuring they are completely free of epoxy.
​
Below are some pictures of my designs, printed parts, the mixing process, and how the parts are intended to be used.


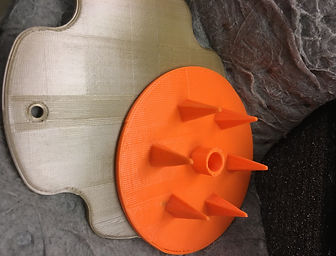
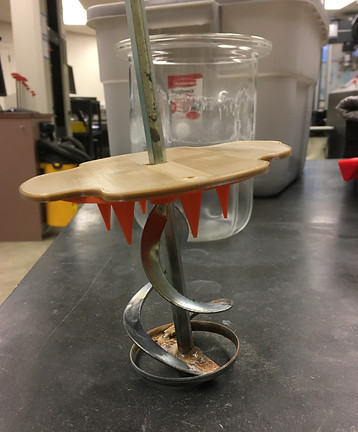


Future Plans
WWU Racing Team
September 2021 marks my 2-year anniversary of being on the team and I don't plan on leaving until I graduate. I will finish the remainder of the school year as the team's Project Manager and have high hopes that I will be able to take our team of students to the SAE Michigan Competition in June of 2022 and perform to the team's greatest ability. This would be the first time our team goes to competition since June of 2019. I have grown to care for this opportunity I have been given by joining this team, and the people I have had the pleasure of working with excites me for future team projects I may work on. I even plan to be an active and helpful alumnus to the team after graduation, like many others that did for me.
​
Senior Year at WWU
The 2021-2022 school year will be my final year of college, perhaps being the most important. I will continue working hard as that is how I got to this point, and I fully intend on taking advantage of what I will learn from my curriculum as well as my Senior Project that will heavily focus on the Plastics and Composites industry. Fall of 2021 will be my first year participating in research within WWU's Plastics and Composites Engineering department. The focus of this research will be to demonstrate a composite recycling process and validate the recycled components in relevant applications such that commercial production of recycled carbon fiber will reduce overall price and expand availability to a wide array of industries. My Senior Project is also related, as I will be continuing from my research and am now finding applications for recycled carbon fibers combined with a thermoset matrix.
​
Career Post-College
At this time, I am open to anything engineering related. As of 2022, I have had 8+ years of academic experience using 3D CAD software for various design projects and become gained a lot of skill and knowledge in the area. I have been very open-minded as to what I want to spend the rest of my life doing, and through school I have become very interested in the composites industry as well as things like the injection molding process. What I have learned from the Plastics and Composites program has been incredible and has shown me how relevant it is in hundreds of applications across the world.